Made in CHina
Mold Making Services
Tebart specializes in mold design, analysis, production, mold testing and injection molding production, achieving maximum efficiency at each stage, carried out by a highly skilled team using the most advanced equipment. This allows us to quickly convert 3D part data into high-quality injection molded components in customer-specified resins, with numbers ranging from tens to hundreds of thousands.
Based on this experience, we have developed one of the most streamlined and repeatable in-house mold manufacturing processes, allowing us to typically ship the first formed part in 15 working days or less.
What is Mold Making?
Plastic injection molds are usually made of hardened or pre-hardened steel, aluminum, and/or beryllium copper alloys. Steel molds cost more, but are often favored because of their high durability. Hardened steel dies are heat treated after machining and they are excellent in terms of wear resistance and service life.
Many steel molds are designed to handle more than a million parts during their lifetime. For smaller volumes, pre-hardened steel dies offer an option with lower wear resistance and lower cost.
On the other hand, the cost of aluminum molds can be greatly reduced, but they are usually not suitable for mass production or parts with narrow dimensional tolerances. However, when designed and manufactured using computer numerical control (CNC) machines or electric discharge machining (EDM) processes, aluminum molds can economically produce tens to hundreds of thousands of parts.
Copper alloy inserts are sometimes used in mold areas where rapid heat dissipation is required. This can reduce cycle time and improve the aesthetic quality of the part.
Our Advantages
We have reduced the typical mold manufacturing time of more than 6 weeks to a few days. And because we also do the molding in-house, the typical transfer time from mold production to the molding shop can be reduced to a few hours in some cases.
Precision production equipment
Industry-leading CNC and EDM equipment, mold standard accuracy up to +/- 0.01mm
Excellent finish
Manual table for excellent surface finish, can apply a variety of customized textures
High quality raw materials
High stability alloys and high-quality die parts are used to ensure stable operation during the forming process
Very competitive quality
Mold frame and cavity are made of first-class steel, refined by high-precision equipment
Fast delivery time
Internal mold production services, urgent project samples can be shipped within 15 working days
High complexity geometric parts
It involves complex ribbing, cladding forming, insert forming, numerous bottom cuts and internal and external threads
Design Analysis
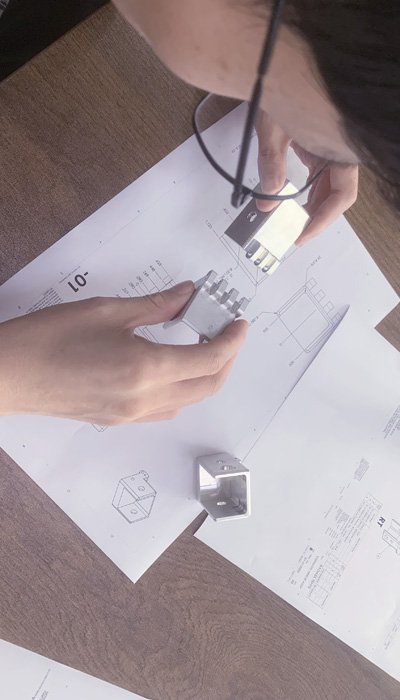
Conduct feasibility analysis
We conduct a feasibility analysis using a DFM report, sharing feedback and offering advice to our customers to prevent production errors. This proactive approach allows us to correct potential failures, reducing costs and ensuring exceptional product quality.
Perform MoldFlow simulation
The latest MoldFlow software enables us to predict plastic part behavior during production by simulating mold placement and temperature control. This simulation is crucial in the concept phase as it helps prevent issues like fuse lines, air pockets, and dents in the final product.
Perform fill analysis
Using state-of-the-art computer-aided design (CAD) software and computer-aided engineering (CAE) technology, we can accurately simulate injection molded parts and predict the filling state prior to installation. Uneven mold fillings can change the shape of the finished part. Early MoldFlow analysis can prevent this from happening.
Process of mold manufacture




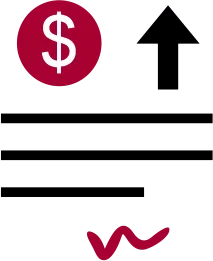
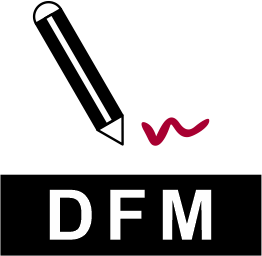

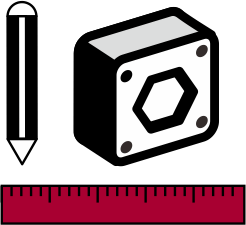
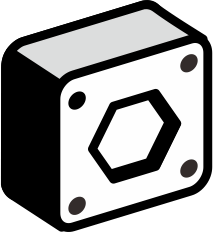
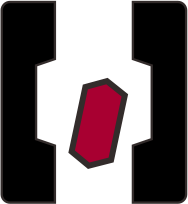
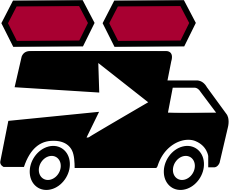
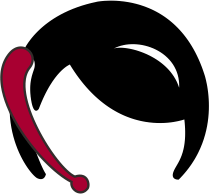
Submit inquiry
Design analysis
Prototype manufacture
Design determination
Mould making
Sample Test
Sample distribution
Confirm mold



Process of mold manufacture
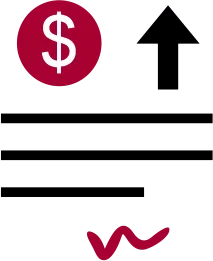
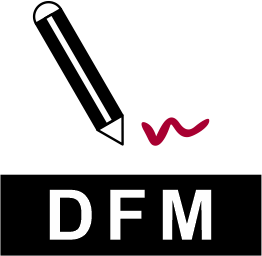
1. Submit inquiry
2. Design analysis

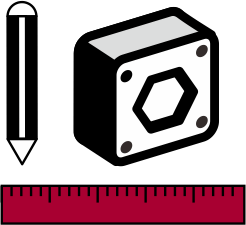
3. Prototype manufacture
4. Design determination
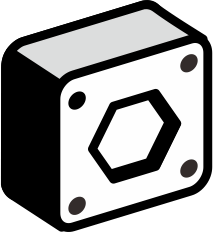
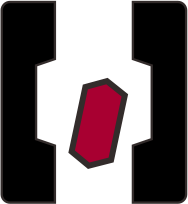
5. Mold Making
6. Sample Test
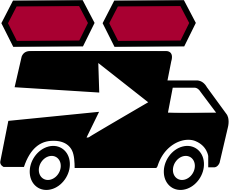
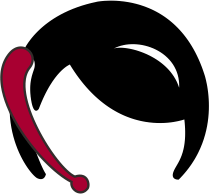
7. Sample Shipping
8. Confirm Sample
Cost optimization
Items | Description |
Design | Excellent part design reduces complexity and eliminates unnecessary costs. |
Tolerance | Injection molded precision parts that require high gloss surfaces also require additional manual grinding after production. This increases mold manufacturing and maintenance costs. |
Valume | The mass production of plastic parts requires highly sophisticated injection moulds. Increasing the number of cavities will increase the production capacity. However, tools with multiple cavities have higher manufacturing costs. |
Size | The larger the part, the more material is needed. The more materials, the higher the cost. |
Production cycle | To achieve short cycles of plastic injection molding, the tool must cool the cavity quickly and evenly. Precision molds speed up the cycle, but also increase the cost. |
Cooling time | The uniformity of the injection mold and the cooling time determine the efficiency of the process. Uniform cooling of the entire cavity allows for the shortest period. The cooling time difference will profoundly affect the mold manufacturing process. |
Mold Materials | Volatile or corrosive plastic injection parts can generate higher temperatures and additional pressure. Die steel will require special material properties to withstand this burden. |
Gate position | Gate placement directly impacts the molded part. If not on the mold side, it may necessitate extra construction for the injection tool. Extensive hot runner system usage can raise mold costs but lower unit prices for molded parts and tool complexity. |
FAQs
Q: How much does the injection mold cost?
A: Prices range from a thousand dollars to tens of thousands of dollars, depending on the complexity of the mold you want.
Q: Is injection molding environmentally friendly?
A: Modern injection molding processes are more environmentally friendly. They attribute this to efficient machines, as well as durable thermosetting polymers that can withstand extreme temperatures. However, this does not mean that injection molding is absolutely safe for the environment. It also releases harmful gases that contribute to the greenhouse effect, but modern injection molding can well control this.
Q: Is there a way to reduce injection molding costs without compromising product quality?
A: Yes, there is! You can do this by reducing or removing unnecessary features like company logos, textured surfaces, and molded part numbers.